China Aluminum sheet and plate Manufacturer
HXSCO is a leading aluminum sheet and plate manufacturer and supplier in China. We offer a comprehensive range of high-quality aluminum sheets and plates. All of our sheets and plates meet the stringent standards of the global market. We have an SGS-ISO 9001 certification. It ensures that our aluminum products meet the highest quality and reliability standards. We follow the best practices throughout the manufacturing process.
Our aluminum sheets and plates find applications across various sectors. Some of those include power, aerospace, and transportation. Our aluminum products are known for consistent quality, reliability, and long service life. They have become the preferred choice for many high-quality material applications.
HXSCO, having expertise, excels in standard and custom aluminum sheets and plates. We provide the highest quality aluminum products at competitive wholesale prices. Contact us today to learn more about our aluminum sheet and plate manufacturing. As we are SGS-ISO 9001 certified, you can confidently buy our aluminum products. Rest assured that they meet the highest quality standards.
Contact UsAluminum plate & sheet specification
Standard Specification / GB/T 3880, ASTM B209, EN 485 Alloy and Temper:
AVAILABLE SIZE RANGE | STANDARD WIDTH x LENGTH | |
Dimension Range Thickness: 0.5 ~ 6.0mm for sheet 6.0 ~ 404mm for plate Width: 900 ~ 4,000mm Length: 2,000 ~ 12,000mm | 1000 x 2000mm; 1250 x 2500mm; 1500 x 3000mm; 1020 x 2020mm; 1270 x 2520mm; 1520 x 3020mm; 1219 x 2438mm; 1524 x 3048mm; 1220 x 2440mm; 1200 x 2400mm | |
SURFACE FINISH | SURFACE PROTECTION | |
Mill Finish, Brush Finish, Mirror Finish | Paper Interleaved, Blue PE Film Interleaved, Black and White PVC Interleaved; Laser PVC Interleaved | |
Alloy | Temper | |
1xxx: 1050, 1050A, 1060, 1100, 1200 | O, H112, H12, H14, H16, H18, H22, H24, H26 | |
3xxx: 3003, 3004, 3005, 3105 | O, H112, H12, H14, H16, H18, H22, H24, H26 | |
5xxx: 5005, 5052, 5754, 5083, 5454, 5086, 5182 | O, H111, H112, H22, H24, H26, H28, H32, H34, H36, H38 | |
6xxx: 6061, 6082 | O, T4, T451, T6, T651 | |
2xxx: 2014, 2017, 2024 | T351, T451 | |
7xxx: 7075, 7050 | T6, T651 | |
*H116 and H321 for alloy 5083 are provided as per Mill’s Standard or by agreement |
TYPES OF ALUMINIUM PLATE WE STOCK
wholesale aluminum sheet and plate
Flat Sheets: The Foundation of Possibilities
- Flat aluminum is a flat and smooth aluminum sheet widely used in fields such as construction, home appliances, aerospace, and automobile manufacturing. It is a basic material with good strength, corrosion resistance, and easy processing.
Tread Plates: Navigating Durability with Style
- Tread Plates, also called patterned aluminum plates or anti-slip aluminum plates, have raised patterns on the surface to increase friction and prevent sliding. They are often used on industrial floors, stair treads, car floor panels, and architectural decorations where anti-slip functions are required.
Embossed Sheets: Elevating Aesthetics with Texture
- Embossed aluminum plates are processed by special molds to form various embossed patterns on the surface. This type of plate is beautiful and has the advantages of enhanced strength, anti-slip, and reduced surface wear. It is often used in decoration, building exterior walls, and furniture manufacturing.
Corrugated Sheets: Strength Meets Structural Ingenuity
- The corrugated aluminum sheet has a wavy surface. Its design increases the sheet’s strength and rigidity while maintaining its lightweight characteristics. It is widely used in roofs, walls, fences, and architectural decoration, providing structural support and adding aesthetic effects.
Perforated Sheets: Balancing Form and Function
- Perforated aluminum plates are made by punching holes on aluminum plates according to a certain spacing and shape and have good air permeability and decorative effects. They are widely used in fields such as building curtain walls, interior decoration, audio equipment, and protective covers, which can meet functional requirements and have aesthetic effects.
Anodized Aluminum Sheets: Durability in Vivid Hues
- Anodized aluminum plates are electrochemically treated to form a thick and dense oxide film on the surface of the aluminum plate to enhance its corrosion resistance, wear resistance, and decorative properties. It is often used in fields with high requirements on surface quality, such as electronic product casings, architectural decoration, and automotive parts.
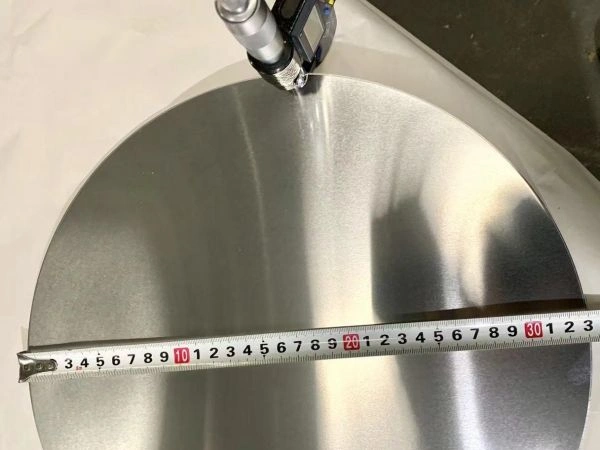
Aluminium Plate fabrication – cut to size
As an aluminum sheet supplier, we specialize in aluminum sheet manufacturing. Our cut-to-size service sets us apart. It ensures minimal waste and precise dimensions for your projects. There is no minimum spend required. Our range includes standard rectangular and flat plates. It also includes specialized shapes like round and polygonal ones. Plus, our reliable delivery ensures you get your customized aluminum plates promptly. So we empower your business with quality materials when you need them.
custom aluminum plate and sheet – Grades
- 1. 1100
It is commercially pure aluminum with excellent corrosion resistance. It offers excellent workability and high conductivity, making it ideal for chemical and food handling. - 2. 2024
It is solid and has good fatigue resistance. Aerospace applications commonly use it where a high strength-to-weight ratio is essential. - 3. 3003
They are excellently corrosion-resistant, offer decent workability, and are moderately intense. They find their applications in Chemical equipment, storage tanks, and architectural products.
- 4. 5052
High fatigue strength and excellent corrosion resistance, particularly in marine environments. Suitable for marine, automotive, and aircraft applications. - 5. 6061
It is a standard alloy with excellent mechanical properties, weldability, and corrosion resistance. It is used in structural applications, automotive, and marine environments. - 6. 7075
They are high strength and hardness, with good fatigue resistance but lower corrosion resistance. They are primarily standard in aerospace applications and other high-stress environments.
- 7. 5083
Excellent performance in extreme environments, particularly resistant to seawater corrosion. Ideal for marine and industrial applications.
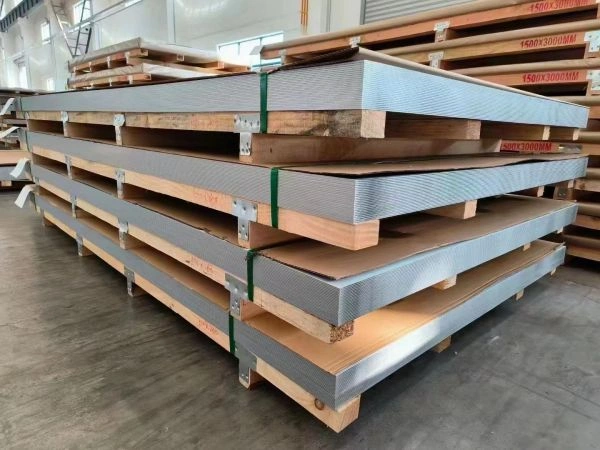
Advantages of Our aluminum plates and sheets
High Strength-to-Weight Ratio
Aluminum alloys, like 7075-T6 and 6061-T6, provide excellent strength. They are much lighter than steel. This high strength-to-weight ratio is crucial in industries. Examples include, aerospace, automotive, and marine. In these industries, reducing weight can improve fuel efficiency, performance, and load capacity.
Corrosion Resistance
Aluminum naturally forms a protective oxide layer that resists corrosion. Alloys like 5083-H116 are made to withstand harsh environments due to oxide layer formation. They remain in good condition, even in marine and industrial settings with saltwater.
.
Excellent Workability and Formability
Aluminum is known for its ease of machining, forming, and welding. Alloys like 3003-H14 and 5052-H32 are known for their workability. This feature makes them ideal for complex shapes and intricate designs.
Electrical and Thermal Conductivity
Pure aluminum and certain alloys have excellent electrical and thermal conductivity. For example, 1050-H14 and 1350 are such alloys. This makes aluminum ideal for heat dissipation and electrical conductivity.
Recyclability
Aluminum is 100% recyclable without losing its properties. Recycling aluminum requires only about 5% of the energy used to make primary aluminum. This makes it a sustainable and eco-friendly material.
Durability and Longevity
Aluminum resists corrosion and has excellent strength. So, it lasts a long time, even in challenging places. It does not degrade quickly, maintaining its properties over time.
Common uses for aluminum sheets and plates
Aerospace Industry
Application: Aircraft structures, wings, fuselages, and other critical components.
- Aluminum Alloy: 7075-T6
- Advantages: The aerospace industry values 7075-T6 aluminum. It has a high strength-to-weight ratio and excellent fatigue resistance. Aluminum is much lighter than steel and many other materials. This feature makes it great for applications where cutting weight is needed without losing strength.
Marine Industry
Application: Boat hulls, ship superstructures, and offshore platforms.
- Aluminum Alloy: 5083-H116
- Advantages: Aluminum alloy 5083-H116 is highly corrosion-resistant, especially in saltwater environments. This makes it preferable over steel, which is prone to rust. It is also durable and lightweight, improving marine vessels’ fuel efficiency and load capacity.
Automotive Industry
Application: Body panels, chassis, and engine components.
- Aluminum Alloy: 6061-T6
- Advantages: 6061-T6 aluminum is used for its good mechanical properties. These include corrosion resistance and lightweight. The automotive industry benefits from aluminum. It improves fuel efficiency and performance. Not only this, but it also reduces emissions compared to heavier steel components.
Construction Industry
Application: Building facades, roofing, structural frames, and window frames.
- Aluminum Alloy: 3003-H14, 6063-T5
- Advantages: Aluminum 3003-H14 is widely used for its excellent corrosion resistance and workability. 6063-T5 offers good extrudability and finish for architectural applications. Aluminum is resistant to weather and other environmental factors. Not only this, but it is super lightweight. These characteristics make it ideal for construction.
Electrical Industry
Application: Busbars, electrical enclosures, and heat sinks.
- Aluminum Alloy: 1050-H14, 1350
- Advantages: Pure aluminum (1050-H14 and 1350) has excellent electrical conductivity. It is about 61% of copper’s conductivity but significantly lighter. These properties make aluminum preferable for electrical applications with critical weight and conductivity.
Packaging Industry
Application: Foil packaging, beverage cans, and food containers.
- Aluminum Alloy: 1100-H14, 3004-H19
- Advantages: Many industries use aluminum 1100-H14 due to its corrosion resistance and workability. Similarly, 3004-H19 offers higher strength. Aluminum packaging is lightweight and recyclable. It also provides an excellent barrier to light, oxygen, and moisture. These qualities make aluminum superior to many materials in preserving food and beverages.
FAQs About Aluminum Sheet and plate Supplier – HXSCO
The primary difference between aluminum sheets and aluminum plates lies in their thickness:
- Aluminum Sheet: Refers to aluminum material with a thickness ranging from 0.2 mm to less than 6 mm. Applications that require thin material use sheets. Examples include automotive body panels and roofing.
- Aluminum Plate refers to aluminum material with a thickness of 6 mm or greater. Plates are used in applications that require more structural strength and rigidity. Examples include aerospace components, heavy machinery, and shipbuilding.
Welding aluminum can be more challenging than welding steel due to aluminum’s specific properties. However, it is feasible with the proper techniques and equipment. Key points include:
- Preparation: You must clean aluminum thoroughly to remove oxide layers and contaminants.
- Welding Methods: TIG (Tungsten Inert Gas) and MIG (Metal Inert Gas) welding are used for aluminum. TIG welding offers better control for thin materials, while MIG welding is faster for thicker ones.
- Skill Level: Welding aluminum requires a high level of skill. Aluminum’s higher heat conductivity and lower melting point make it challenging. If not properly managed, these characteristics can cause burn-through or warping.
The strength of a 3 mm aluminum plate depends on the alloy and temper:
- Aluminum Alloy 6061-T6: It has a yield strength of about 240 MPa (35,000 psi). Its ultimate tensile strength is about 310 MPa (45,000 psi).
- Aluminum Alloy 5052-H32: It has a yield strength of about 193 MPa (28,000 psi). Its ultimate tensile strength is around 228 MPa (33,000 psi).
The figures show that a 3 mm aluminum plate can be super substantial. Depending on the specific alloy, it is suitable for various applications.
The rigidity of an aluminum plate depends on the application and the loads it will encounter. Determining the necessary thickness requires engineering calculations. The process of calculations usually relies on the expected loads and spans:
- Beam Theory: Use formulas from the Euler-Bernoulli beam equation. It determines the required thickness for rigidity.
- Standard Practices: Plates often need to be significantly thicker for structural applications. A plate 10 mm or thicker may be necessary for heavy-duty usage requiring high rigidity.
Aluminum plates are generally not as strong as steel on a per-volume basis:
- Strength-to-Weight Ratio: Aluminum has a higher strength-to-weight ratio than steel. This characteristic makes aluminum advantageous for applications where weight is a critical factor.
- Absolute Strength: Steel is generally solid. It has higher tensile and yield strengths than most aluminum alloys. For example, mild steel has a yield strength of around 250 MPa. On the other hand, 7075-T6 aluminum has a yield strength of around 503 MPa. Remember that 7075-T6 aluminum is one of the strongest aluminum alloys. The most robust aluminum alloy has a slightly higher yield strength than mild steel.
Aluminum does not rust because it does not contain iron. Instead, aluminum forms a thin oxide layer on its surface. This layer helps prevent further oxidation.
- Oxidation: The aluminum oxide layer is thin, strong, and protective. It safeguards the material from rusting.
- Corrosion: Aluminum doesn’t rust but can corrode in some conditions, such as when exposed to saltwater or acid. Specific aluminum alloys or coatings can enhance corrosion resistance.
The strongest commonly available aluminum alloys are from the 7xxx series:
- 7075-T6: This alloy is well known for its high strength. Its yield strength is about 503 MPa (73,000 psi), and its ultimate tensile strength is about 572 MPa (83,000 psi). Aerospace and other high-stress applications widely use it.
- Application: 7075 is preferred where high strength is required. However, it is also more susceptible to corrosion than other aluminum alloys. Hence, additional protective measures might be needed in specific environments.